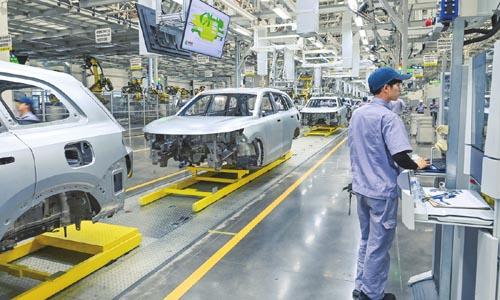
In global supply chain restructuring, China’s advantage is manpower
Ding Gang
There have been two major industrial news stories recently. One is Taiwan Semiconductor Manufacturing Company (TSMC)’s investment of $40 billion in the US to build an advanced chips factory, with Biden attending the groundbreaking ceremony; The second is the US and EU using the carbon emission issue to propose new tariffs on steel and aluminum from China. The US and European supply chain restructuring is accelerating.
Some may ask if supply chain reconfiguration will have strong side effects on the US, Europe and the global economy. The tariff increase, in particular, will have a greater impact on EU industries and could potentially trigger long-term inflation. But that is precisely what makes this supply chain reconfiguration different.
From the policy-making level, the US and EU are determined about restructuring. Washington is determined to reconfigure it, and sees it as a “life and death battle” for the future of the US to maintain its global dominance. The US is prepared to suffer side effects, which include backlash from its containment policies, even a trade war against China.
While we debate whether the US will survive this once in decades inflation and fall into a recession, the process of restructuring and re-industrialization of the US economy has already begun.
Furthermore, as China begins to emerge from the epidemic and make every effort to recuperate its economy, the globalization we once knew has changed significantly.
Since China’s accession to the WTO in 2001, Chinese manufacturing has grown and joined the global industrial chain, gradually becoming the most important part in the global supply chain. China has become a rising power, and has gone hand in hand with its rising position in the supply chain.
More importantly, China has built a strong manufacturing workforce ever since.
The current round of reconfiguration does not mean that anti-globalization will become mainstream. But the reconfiguration has led to a change in the structure of globalization on which China’s rise has depended upon, and the impact this will have on the Chinese economy may vary widely. Both at the high end, with chips, EV batteries, biotechnology, etc., and at the middle and high end, with textiles, photovoltaics, steel and aluminum, etc.
This is not just a shock to China’s imports and exports, but will also have a significant impact on China’s domestic industries and the economy as a whole. Some foreign media predict that this process will continue until 2030 and that it will not be smooth sailing for all the major industrial countries, that is to say, through strong pain, it will not only be a test of the economy’s ability to innovate, but also a test of its ability to withstand when the economy falls.
At present, major industrial countries have roughly the same path to reconstruct their supply chains, for example, to improve the competitiveness of leading industries, to achieve as much self-sufficiency in the whole supply chain as possible for key industries, to improve investment and innovation in key areas, and to nearshoring- and friendly shoring industries, etc.
However, all of these cannot be done without people, without a willing workforce who is to undertake R&D and upgrade manufacturing capabilities.
The competition of supply chain restructuring is first of all the competition of people, the competition of labor force.
And as far as human resources are concerned, China has certain strengths, and it has a multi-level labor force across the whole of industry.
Think about it, why is it difficult for India, our neighboring country with a large population, to replace China in the manufacturing sector? Because of the lack of infrastructure, lack of logistics, lack of legal environment, after all, most importantly, because they do not have the same quality workforce as China has. And here lies the main challenge facing the US and Europe in reconfiguring their supply chains.
In the aspects of the competition in manufacturing in the major industrial countries that China already has a leading position, it is because in those aspects, human resources have won.
The key now is how to consolidate and continuously improve the workforce of China’s manufacturing industry, especially the human resources of small and medium-sized enterprises. This should be the focus of economic recovery after the epidemic. Therefore, while the country increases its investment in the real economy, it needs to focus on how to preserve and upgrade its human resources.
The writer is a senior editor with People’s Daily, and currently a senior fellow with the Chongyang Institute for Financial Studies at Renmin University of China